Navigating Semiconductor Supply Chain Challenges Amid Global Tariff Risks
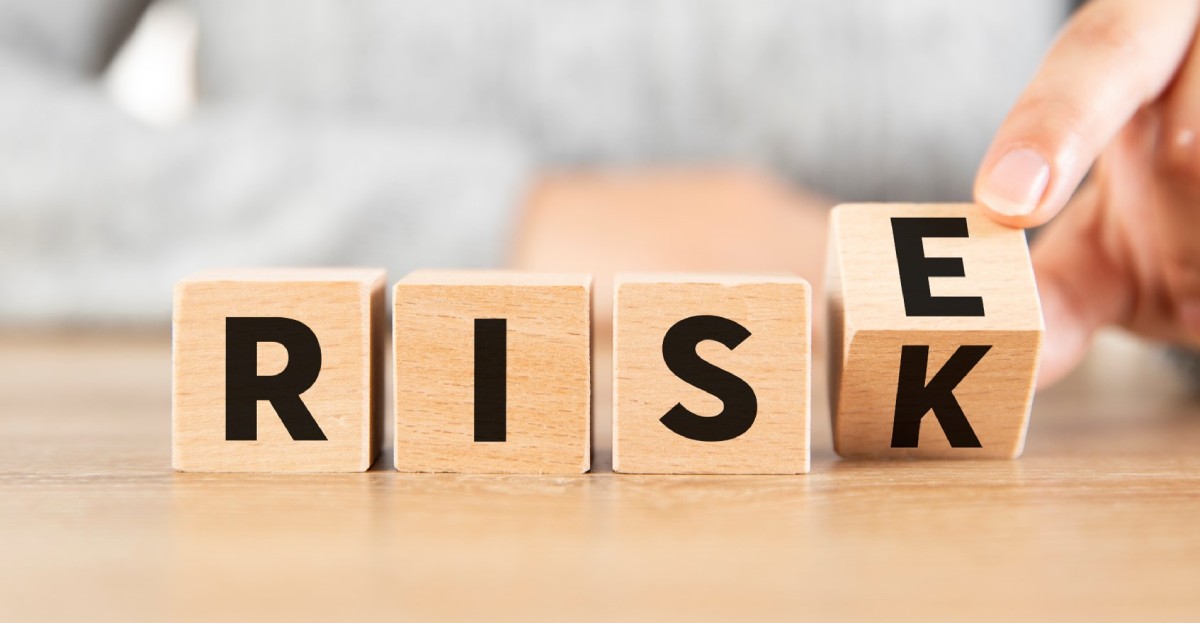
Looking ahead to 2025, the embedded system market is projected to reach $116.2 billion, driven primarily by automotive and consumer electronics. Non-volatile memory (NVM) is set to grow to $112.48 billion, fueled by the rise of AI, 5G, and edge computing. Meanwhile, the DRAM market will experience ongoing shifts as AI-driven demand for advanced memory competes with supply challenges in older generation components.
At the same time, the U.S. electronics manufacturing industry is facing mounting pressure. Recent announcements of global tariff policies—particularly those targeting key semiconductor-producing nations—have heightened risks and complicated sourcing strategies for critical components. With the semiconductor supply chain already stretched thin due to shortages lingering since the pandemic, procurement teams must now consider not only lead times and capacity constraints but also the rising costs driven by tariffs and sanctions.
With geopolitical tensions on the rise, rising costs, and supply chain vulnerabilities, industries from consumer electronics to critical infrastructure must prepare for potential shocks. For Original Equipment Manufacturers (OEMs), the ability to anticipate these risks and implement strategic countermeasures will be key to maintaining competitiveness.
Rising Costs and Supply Chain Volatility
The first source of price spikes is tariffs. Heavily discussed in the media, the prospect of high tariffs on semiconductors from Taiwan—which produces approximately 60% of the world’s chips—could drive up costs for U.S. manufacturers across. These price hikes would inevitably trickle down to end consumers. President Trump proposed to impose tariffs of up to 100% on semiconductors from Taiwan, which supplies 44.2% of U.S. logic chip imports and 24.4% of memory chip imports, making it a cornerstone of the U.S. electronics supply chain. If high tariffs were imposed, the resulting cost increases could raise logic chip prices by as much as 59%, significantly impacting industries reliant on semiconductors, from automotive, and artificial intelligence (AI), to consumer electronics. Moreover, U.S.-headquartered ICT firms, which account for 65% of global demand for fabless semiconductor manufacturing, could see operational costs rise sharply, potentially pushing them to move production offshore.
Next to tariffs imposed on specific Asian countries, the balance between supply and demand continues to heavily determine pricing. While much of the semiconductor industry focuses on cutting-edge nodes, many sectors—including industrial and defense—continue to rely on previous-generation memory components and chips in general. With limited global capacity for these legacy nodes, supply shortages could intensify, leading to production delays and cost overruns.
Geopolitical and Trade Risks
The U.S. is walking a tightrope with its tariff policy on Taiwanese semiconductors. If, for example, tariffs on Taiwanese chips were set higher than those on Chinese semiconductors, the policy could inadvertently benefit China’s semiconductor industry by making its exports to the U.S. relatively cheaper. Such an imbalance could escalate into a broader tariff war, further destabilizing the global semiconductor market. Meanwhile, China’s export restrictions on essential minerals like gallium and germanium pose additional threats to the semiconductor supply chain, adding another layer of complexity for companies navigating these geopolitical risks.
In response to escalating trade tensions, manufacturers are shifting production to Southeast Asia and Mexico to reduce dependence on single-source suppliers. While this strategy offers long-term stability, it introduces new logistical hurdles and higher operational costs.
Domestic Production Delays
The U.S. CHIPS Act was designed by the previous administration to bolster domestic semiconductor production, but progress has been sluggish. TSMC’s Arizona fab project, initially slated for earlier completion, has been pushed to 2028 due to labor shortages, high equipment costs, and complex permitting requirements. Compounding the issue, the U.S. semiconductor industry faces 58,000 unfilled jobs, making it difficult to scale domestic manufacturing at the pace required.
Strategies for Mitigation
To counter these challenges, U.S. electronics manufacturers are deploying several key strategies:
- Supply Chain Diversification: Companies are reducing reliance on Taiwan by working with fabs in North America, Europe, and Southeast Asia. Multi-sourcing strategies ensure redundancy, with firms qualifying 2-3 suppliers per critical component to maintain production across multiple facilities.
- Inventory Strategy Overhaul: Manufacturers are transitioning from just-in-time (JIT) inventory models to more costly buffer stock strategies, especially for legacy semiconductors.
- Collaborative Forecasting: To improve supply chain visibility, companies are sharing 12-month forecasts with key suppliers, allowing for better anticipation of disruptions and proactive adjustments to production schedules.
- Design & Manufacturing Flexibility:
- Pin-to-Pin Alternatives: 78% of OEMs now design circuit boards with interchangeable components, enabling rapid substitutions when shortages arise. NVIDIA, for example, has engineered its latest GPUs to support four different memory chip variants.
- Retrofit Programs: Extending product lifecycles through certified refurbishment initiatives is helping manufacturers cut new chip demand by 15-20% annually.
The Road Ahead: Preparing for the Unexpected
While tariffs are being considered as a means to boost domestic semiconductor production, they also pose risks of short-term instability and rising costs for U.S. manufacturers. The industry remains heavily reliant on Asia, with 92% of silicon wafer production still concentrated in the region. To stay competitive, OEMs must strike a balance between operational agility and proactive policy engagement. The semiconductor supply chain will likely remain unpredictable in the coming years, with global tariff policies continuing to play a major role. Staying informed on geopolitical developments and building resilient supply chain strategies are no longer optional—they’re essential for maintaining a competitive edge.
OEMs and procurement specialists who take a proactive approach will be better positioned to weather disruptions, minimize costs, and maintain continuity in production. In this rapidly evolving landscape, the companies that succeed will be those that remain agile, leverage strategic supplier partnerships, and maximize policy incentives to ensure a resilient and sustainable semiconductor supply chain.
SMARTsemi is your supply chain partner for DRAM components, eMMC solutions, and SD/microSD Flash Memory Cards for long-life applications. With 20+ years of industry experience, we understand your challenges and have aligned our priorities with yours to simplify your memory chip supply chain for the long run. We know what you need before you need it. Get a jump start and request a sample today.